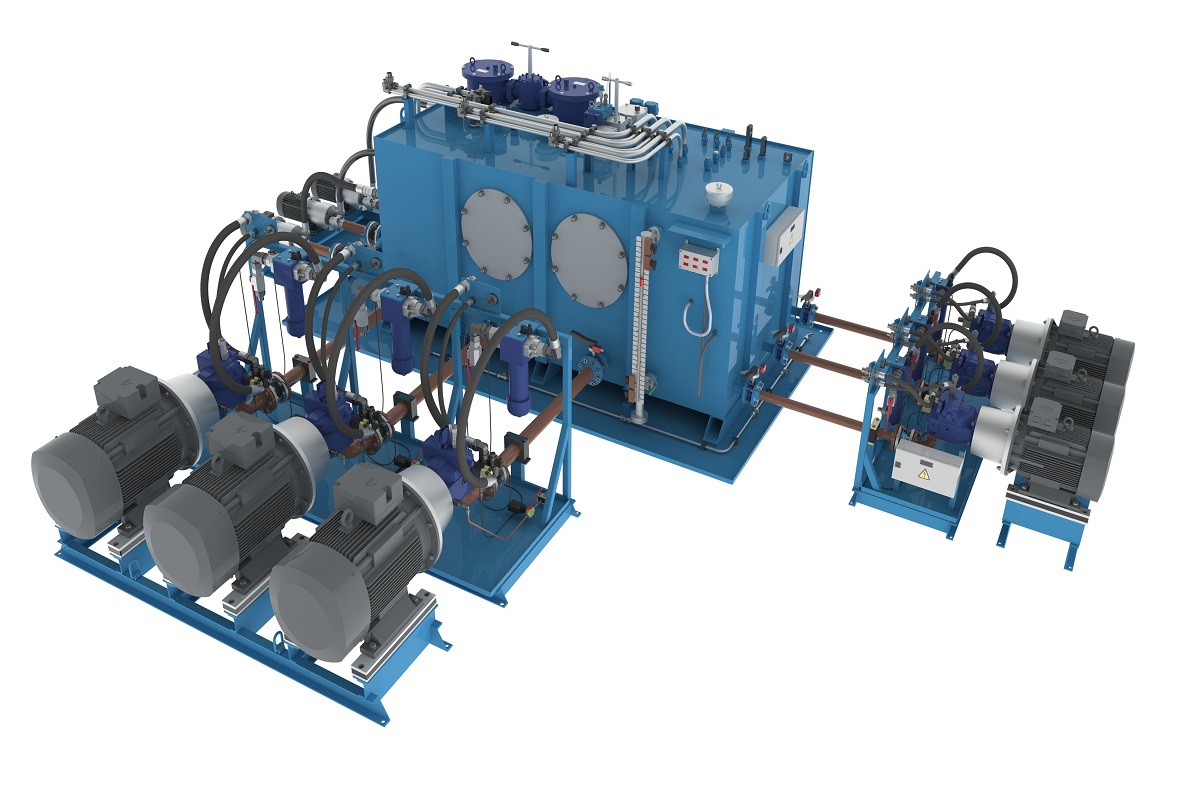
Industry Insights
Accelerating product development for fluid power systems
The Solid Edge portfolio of software solutions enables manufacturers to respond to major trends impacting the fluid power systems and components industry with the use of digital 3D models.
Using a digital model as the basis for product development
Manufacturers of fluid power systems and components are facing an increasing number of challenges, including expanding global competition, ever-increasing product complexity and growing demands for product reliability and energy efficiency. Many businesses are reacting to these external pressures by investing in a digital transformation across product design and development areas.
Advances in engineer-to-order processes, generative design, additive manufacturing and integrated electromechanical design help facilitate the development of highly efficient and reliable fluid power systems. These technological innovations use data to create a 3D digital model, a virtual clone of real products, which allows developers to evaluate and manage complex products.
A detailed 3D digital model of a proposed product can be used as the basis for all areas of product development. Software tools can accelerate product development while, at the same time, optimizing designs and reducing costs. The Siemens Solid Edge software portfolio enables digital transformation for any size business.
Capabilities
The Solid Edge Advantage
Using Solid Edge improves product development performance in these key areas:
Digitalize engineering processes. Digitalize your entire product development process and transform your business. Streamline engineering processes with 3D digital models. Add intelligence to 3D models throughout the product development lifecycle.
Visualize design intent. Communicate the value of new products to potential customers using photorealistic images and animations prior to manufacturing with 3D rendering. Validate designs in real-world settings using augmented reality.
Respond quickly and accurately to RFQs. Convey specific content for request for quote (RFQ) responses using 3D visualization and paperless drawings available in Solid Edge. Quickly create custom product designs using configure-to-order (CTO) and engineer-to-order (ETO) processes.
Speed mechanical design with 3D CAD. Work directly with design geometry and make changes instantly. Use next-generation design technologies, such as convergent modeling capabilities that automatically combine mesh-based models with b-rep formatted models.
Streamline P&ID and piping design. Capture design intent and/or logic in a 2D piping and instrumentation diagram (P&ID). Create a bill of materials for required components early in the design process. Drive the creation of piping components in 3D and route piping around 3D mechanical assemblies.
Enable electromechanical collaboration. Use data-driven automation to efficiently route electrical wiring within a limited space. Validate circuit performance with specific electrical design tools. Minimize the need to create physical prototypes to validate electromechanical performance.
Optimize kinematic and dynamic behavior. Simulate motion characteristics to understand a design’s dynamic function using Solid Edge assemblies. Minimize the cost and time required to build physical prototypes to validate dynamic performance
Analyze stress and vibration. Optimize designs prior to manufacturing. Simulate vibration levels during product operation using harmonic response analysis. Use Solid Edge Simulation for static, dynamic and fatigue analysis. Use Simcenter Femap for more complex analyses.
Simulate fluid performance in components and systems. Examine trends and eliminate less desirable options early in the design process using computational fluid dynamics (CFD) analysis in Simcenter FloEFD for Solid Edge. Analyze and optimize fluid flow in complete systems with Simcenter Flomaster.
Manufacture accurately and efficiently. Create machining toolpaths based on digital models to ensure accurate and efficient manufacturing processes using Solid Edge CAM Pro. Reduce errors and rework in manufacturing.
Prepare components for 3D printing. Minimize the need to maintain a large inventory of spare parts using in-house 3D printers. Manufacture small-volume parts efficiently using additive manufacturing after using solid Edge to validate designs for successful 3D printing.
Manage project and engineering changes. Access and track design, analysis and manufacturing data and processes using integrated design management tools build into Solid Edge. Speed new product development and time to market with scalable data and process management capabilities.
Manage customer requirements and industry regulations. Manage customer and regulatory requirements using requirements management. Make requirements easily visible to design engineers and track fulfillment of these requirements.
Collaborate with customers and suppliers. Collaborate with suppliers and customers using free, cloud-based collaboration tools that provide browser-based access to multi-CAD data. Protect intellectual property using auto-simplify capabilities to remove internal features before sharing your designs.
Install and maintain. Create interactive 3D work instructions that clearly communicate the correct manufacturing, installation and maintenance procedures for your designs. Solid Edge technical publication solutions easily incorporate design changes, ensuring that published documents reflect the current product.
With 3D CAD, simulation, electrical design, manufacturing and data management capabilities, Solid Edge provides an integrated portfolio of affordable and easy-to-use solutions to help you rise to new challenges for product development of fluid power systems and components.