Thermal appliance firm improves design data management and manufacturing
Thermal appliance firm improves design data management and manufacturing
Rinnai Korea uses Teamcenter and Solid Edge to enhance competitiveness and save over USD$1 million annually.
Leading the thermal and gas appliances sector
Rinnai Korea is a thermal appliance company that develops and manufactures cooking, hot-water heating, and commercial equipment, and supplies gas stoves, ovens, gas boilers, water heaters, and commercial kitchen equipment. Based on 40 years of accumulated technology know-how, Rinnai Korea provides best-in-class products and services, leading the kitchen and hot water heating market segment in Korea. With the slogan of “Quality is Our Life,” Rinnai Korea provides safe, convenient, and eco-friendly products that are comfortable to use.
Seeking an advanced design environment
Rinnai Korea recently began to improve its data-sharing management system so it can accurately share the latest design drawings and bill-of-materials (BOM) in real-time.
The company is also working to improve its ability to collaborate so its design drawings can be used safely and quickly by external parties, including partners at service sites. The ultimate goal is to build an integrated design environment that can facilitate the process.
Previously, Rinnai Korea had to manage the design data of each team within a folder structure on its own file server and manually input updated information between systems. However, since managing data such as design drawings and BOM requires manual work, it was difficult to provide accurate information in a timely manner in case of inconsistency between systems or human errors.
In particular, it was hard to identify the original copy, manage a tracking history of changes in a file and verify and use the output as designers distributed and managed the output needed for tasks such as design drawing files in multiple locations, including a system, file server, and local network; and arbitrarily modify and delete files in shared folders. Also, since the BOM was not automatically linked to the system that needs it, that data had to be entered into the system manually based on the information designed on Solid Edge® software, which caused problems because the changes in design were not shared in real-time. Items with delayed schedules were not immediately visible, making it difficult to respond in time and manage project schedules.
It was also difficult to share and use design drawings at service sites with partners. Security was compromised as design drawings were shared externally in emails, and even if design drawings were shared, it was difficult to inquire about the inventory of components or use-related design drawings at service sites.
“Rinnai Korea sought to create an integrated design environment that can facilitate design work by improving the management system of data sharing and innovating the collaborative system,” says Eungkyu Kim, Rinnai Korea’s manager of information system department.
“By building a system for accumulating and real-time sharing of consistent data, we have established a design environment where all data is managed collectively in a digital environment,” says SangHoon Cho, chief information officer (CIO), Rinnai Korea.
Therefore, Rinnai Korea aimed to build an advanced and integrated design environment in which all design data can be collectively managed in a digital environment by establishing a system that enables consistent data accumulation and real-time sharing. To this end, the company adopted Teamcenter® software, Siemens’ digital lifecycle management solution; Solid Edge, a product development tool portfolio and the Solid Edge technical publications, a solution that enables rapid creation of a variety of illustrations and technical materials. All three products are part of the Xcelerator™ portfolio, the comprehensive and integrated portfolio of software and services from Siemens Digital Industries Software.
Improving design data management and manufacturing processes
“With Siemens Digital Industries Software solutions, we have been able to create an integrated design environment and an efficient collaborative system and improve the overall process of design data management and manufacturing,” says Kim. Moreover, the company has gained an edge in the market by improving data management efficiency, reducing overlapping tasks that occur in many cases, improving service quality, reducing product development time, and shortening product lifecycles.
Using Teamcenter has allowed Rinnai Korea to improve service quality by establishing an integrated design environment. Siemens Digital Industries Software’s Teamcenter solution provides the infrastructure for collaboration and product lifecycle management (PLM). When Solid Edge is used for design, the data is systematically managed in Teamcenter, including changes in design data. This data is transferred to the BOM management system. The BOM data can also be systematically managed using features, such as copying, comparing, changing attributes, and reviewing changes of the BOM, all provided by Teamcenter.
The Teamcenter solution has empowered Rinnai Korea to create an integrated design environment that can be used to easily identify and use linked data, thereby improving the efficiency of data management such as design data, BOM, and technical documents, and reducing working hours and costs. Rinnai Korea saved about 1.2 billion South Korean won (KRW) per year and cut 50 hours of work annually per person in non-development tasks such as drawing search and consistency verification. In addition, seamless data sharing has also helped reduce overlapping tasks, allowing employees to focus on tasks that improve service quality.
Furthermore, Rinnai Korea was able to streamline collaboration and increase productivity using Solid Edge and Solid Edge Technical Publications. Siemens Digital Industries Software’s Solid Edge portfolio provides product development tools that include design, simulation, manufacturing, technical data generation, data management and more. Rinnai Korea created online service documents, including a mobile viewer using Solid Edge 3D model, allowing service workers to use documents such as design drawings on a tablet at service sites. This has facilitated communication with external partners, accelerated product development, and increased productivity.
Read the full case study.
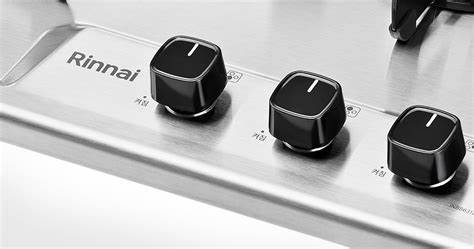