WashTech: Transforming assembly line part cleaning with one-piece flow washing machines
WashTech: Transforming assembly line part cleaning with one-piece flow washing machines
Founded by Mathieu Fresco in 2015, WashTech is an industrial washing company specialized in the design and manufacture of machines for cleaning industrial components. The company has a total of 16 employees and averages $1.8 million in annual sales. Fresco attributes his company’s success to what was, in retrospect, a simple idea: bring the washing process in line with other manufacturing equipment.
Washing industrial parts has historically been expensive and inefficient. Parts are either washed in batches using large machines that clean unevenly, or on conveyor belts, which are also large and consume copious amounts of energy. Fresco knew that there had to be a better approach. Under Fresco’s leadership, WashTech developed a one-piece flow washing machine that can be integrated directly within a manufacturing line, making cleaning parts more efficient and resulting in significant water and energy savings.
“We’ve made a really small, compact machine,” Fresco explained. “And you can integrate it inside your existing production line in between two machines. It can be between a lathe and grinding machine because you don’t want to cross-contaminate the oil with the water. Or it can be just before the assembly line because you want to remove all the contaminants.”
WashTech is one of many companies taking advantage of industrial machinery design capabilities in Solid Edge. The company has been using Solid Edge since its inception in 2015, and recently added modules for electrical wiring design, technical publications, and fluid flow simulation and analysis. With the help of Solid Edge, WashTech has accelerated and improved its overall product development process. The company designs wiring circuits 60% faster, their assembly process is 20% faster, and product testing costs are down 57%. The company’s investment in Solid Edge has also increased design capacity, accelerating time-to-market and enabling them to spend less time and money on physical prototypes to validate their systems.
Simcenter FloEFD for Solid Edge for computational fluid dynamics (CFD) allows WashTech to compare and refine designs without the investment in hardware validation by automating the most onerous CFD steps and helping engineers to immediately prepare and analyze their models. Synchronous technology in Solid Edge provides the company with design freedom and flexibility by combines the speed and simplicity of direct modeling with the flexibility and control of parametric design. With this design flexibility, WashTech can eliminate cumbersome preplanning and avoid feature failures, rebuild issues, and time-consuming rework. Synchronous technology also allows WashTech to share 3D models with other software without import issues and treat multi-CAD data just like native files for seamless collaboration with suppliers and partners. Solid Edge Sheet Metal Design eliminates WashTech’s need to oversize components, resulting in material cost savings. This is a critical factor for WashTech because 80 percent of its designs are sheet metal.
“Synchronous technology is an incredibly powerful tool. Once I learned it, I would never go back to something different.”
— Mathieu Fresco, Founder & Managing Director, WashTech
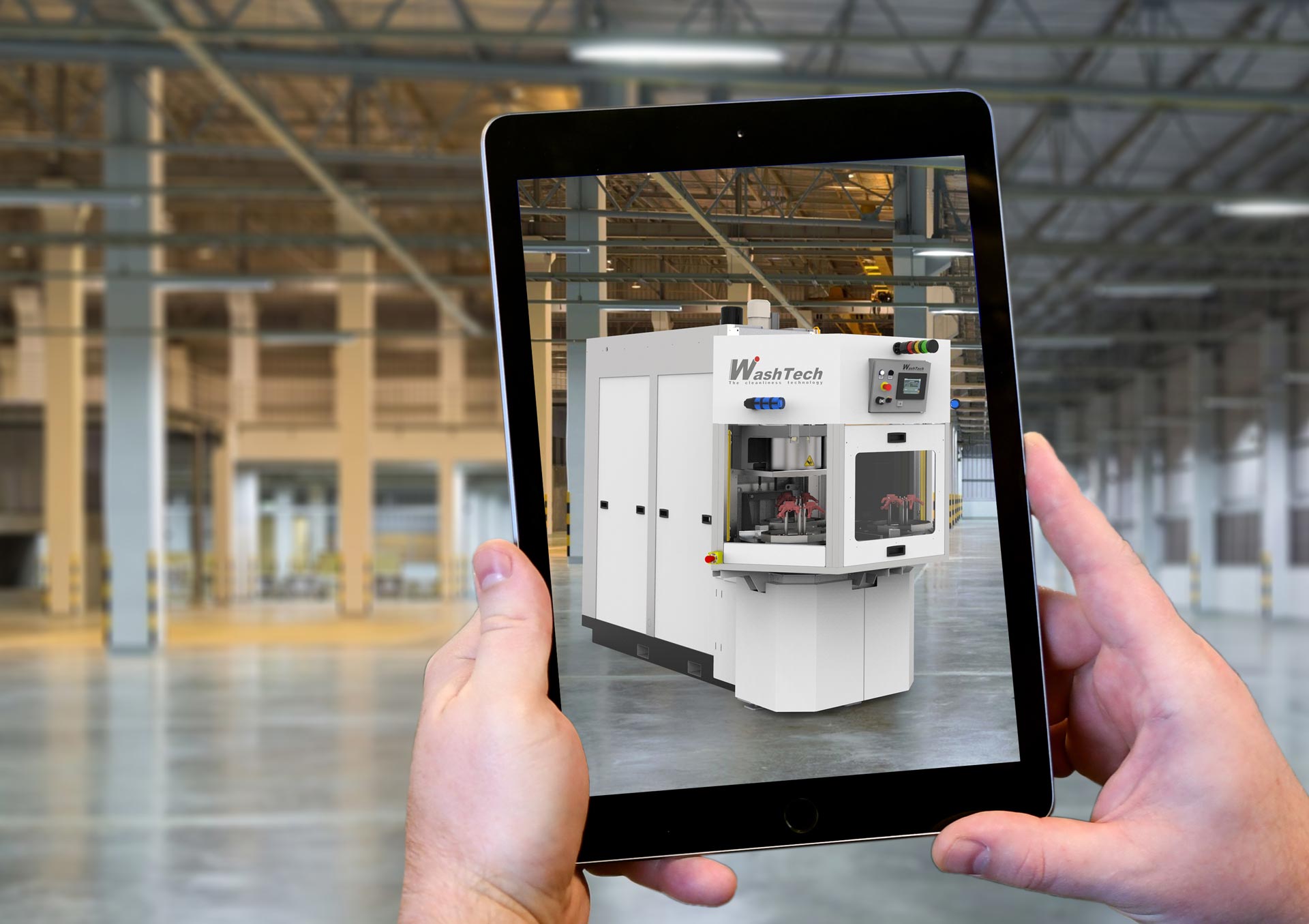